Best Practices in Equipment Management
- Peter Lazar
- Feb 8, 2024
- 10 min read
Updated: Feb 9, 2024
Regardless of whether your official title is 'Equipment Manager,' you might be tasked with inventorying or managing your institution's equipment. This blog covers best practices in equipment management including how to plan and organize, how to optimally configure your equipment management system, how to best perform an inventory and more. Each section provides strategies and insights, enabling you to streamline your equipment management processes for greater operational success.

What is an Equipment Management System?
An equipment management system is a customizable software tool that enhances the management of equipment throughout its lifecycle. Distinct from broader asset management systems, it focuses on managing and tracking equipment, incorporating features such as detailed equipment status flagging and a comprehensive booking system. Key components of these systems include:
Centralized Equipment/Item List: An easily -accessible equipment database. Each item can contain customizable attributes, images and attachments related to them, such as documents.
Booking and Reservation Capabilities: Facilitates various modes of equipment bookings, such as checkouts and reservations, through a user-friendly interface.
Lifecycle Information Tracking: Maintains records of each item from acquisition to disposal, capturing all necessary details.
Maintenance Scheduling and Reporting: Allows for systematic scheduling and tracking of maintenance activities for each piece of equipment.
Notifications and Alerts: are sent when items are booked, coming due, when they are flagged for repair or maintenance and other purposes.
Identification Technology: Utilizes barcodes, QR codes, RFID chips, or NFC tags for quick and accurate equipment identification.
User Rights Management: Safeguards sensitive data and enhances usability with customizable access rights.
What’s in this article
Develop a robust disaster recovery plan
Organize your spaces
Categorize your equipment
Implement the asset management software and begin inventorying
Tailor access rights as you add users
Set up the booking system and perform training
Implement asset flags
Develop an inventory of spare parts
Implement theft and loss prevention techniques
Check the Dashboard daily
Capture costs and maintenance reports related to items
Leverage the reporting and online Spreadsheet for inventory management
Conduct regular maintenance and inspections
Provide ongoing training for equipment use
Maintain ongoing loss prevention strategies
Manage equipment costs effectively
Prioritize equipment upgrades based on usage data
Use the item History
Perform regular audits
Encourage a collaborative environment for feedback
In the sections that follow, we'll unravel the process of selecting, implementing, and maximizing these systems, with a focus on the transformative capabilities of solutions like Scanlily in enhancing how we manage our equipment.
1. Planning and Strategy
With so many asset/equipment management systems available, opting for a dedicated system over spreadsheets is an obvious choice today. The range of solutions vary, but with the emergence of cost-effective yet fully-functional SaaS systems like Scanlily, budget should not be a major concern.
Select your equipment management software based on these key features
Quick and Simple Item Entry and Lookup: A QR-centric approach, such as Scanlily’s, reduces task complexity and the number of steps required, thereby lessening the need for extensive training.
Mobility and Real-Time Visibility: Because your inventory is not at your computer desk, there’s a benefit to using a system which is optimized to allow all actions on mobile, such as in Scanlily. This is in contrast to the more typical approach of older SaaS systems which requires a laptop browser for some of the steps.
Automating Core Tasks via Notifications: A standout feature of modern equipment management software is the automation of essential tasks, including tracking, maintenance scheduling, and reporting. This automation shifts the equipment manager's role to a more reactive one, where the system handles routine monitoring and reminders. For example, Scanlily’s automated systems manage bookings and send notifications for due actions, reducing the need for equipment managers to proactively track every detail. Timely automated alerts for maintenance needs ensure that equipment is maintained effectively, freeing managers to focus on strategic tasks.
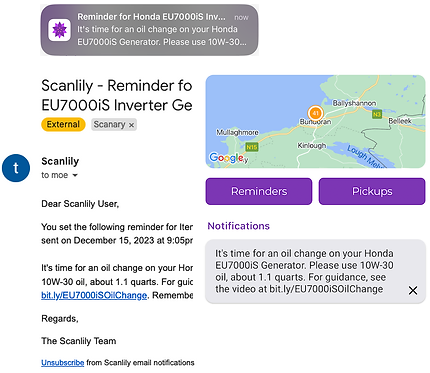
A Robust Bookings System: If people will be borrowing equipment, then consider an equipment management system with a fully-featured booking system that extends beyond simple check-in and check-out capabilities. For example, does the system include a customizable booking agreement with electronic signature that you send to borrowers? And does it easily allow reserving and seeing status via an online calendar?

Customization: Ensure that your chosen system offers customization of item access for specific user groups, similar to Scanlily. Also, verify if it allows for tailored notifications and messages.
A Fully-featured Reporting System: Look at whether the prospective system contains the kinds of reports you need. The ability to easily export data, both for your own reporting and backup, is paramount. Seek out systems offering flexible reporting options, like Scanlily’s Spreadsheet feature, which allows for versatile reporting and manipulation of live data.
Cost: Investing in an enterprise Equipment Management System doesn't have to be costly. For affordable options, consider exploring Scanlily’s pricing.
The above are important features to consider in choosing an equipment management system. The ideal system should meet your organizational requirements and contribute to the efficiency and effectiveness of your equipment management operations. Look for a system like Scanlily that integrates automation, real-time visibility, user-friendliness, and simplicity, showcasing the qualities of a modern equipment management solution.
Develop a robust disaster recovery plan
Have a well-prepared plan for emergencies and unexpected events that may affect equipment availability. Your disaster recovery plan will vary depending on the specific equipment you manage, but it typically includes sections like:
Equipment Recovery Procedures: Outlines steps for repairing or replacing critical machinery post-disruption.
Operational Continuity Plans: Strategies to maintain or quickly resume key operations using alternative resources or methods.
Supplier and Service Contacts: A ready list of essential contacts for quick repair, replacement, or technical support.
Employee Safety and Role Assignments: Procedures ensuring staff safety and clear role distribution during recovery operations.
Communication Strategies: Defined methods for informing staff and stakeholders about disruptions and recovery progress.
Customize each section to meet your organization's specific needs, enabling a prompt and effective response to equipment-related emergencies.
Organize your spaces
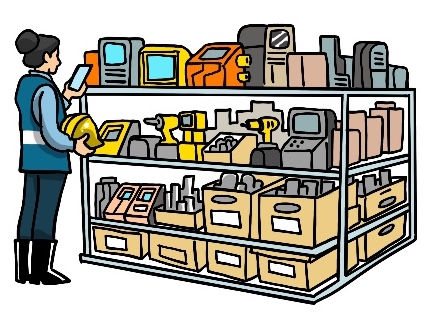
Begin by determining the locations where your equipment is stored. Assign names to various
areas such as rooms, shelves, and bins. These designated areas will serve as the 'Locations' and 'Containers' for your equipment inventory in Scanlily. The software's flexibility in allowing 'containers within containers' simplifies managing multiple levels of hierarchy.
Categorize your equipment
Efficiently categorize your equipment and assets for easy retrieval in the future. For instance, you might categorize some items as 'IT Equipment' and others as 'Furniture.' Scanlily enhances this process by enabling you to define 'Item Types' with shared attributes. For example, the 'Computer' item type could include specific fields like 'Operating System' and 'IP Address,' whereas a 'Vehicle' item type might include 'Model' and 'Mileage.' This tailored approach simplifies data entry because users see only the fields pertinent to the item type being added. However, unlike other systems, use of item types prevents the extra work of individually customizing field lists per item. Similarly, it standardizes and simplifies reporting of information.
2. System Implementation and Inventorying
Moving into the implementation and inventory phase, a system like Scanlily streamlines this process, making it efficient and straightforward. The following describes steps of setting up the equipment management system and diving right in to conducting the inventory.
Implement the asset management software and begin inventorying
With a next-generation SaaS system like Scanlily, the preparation work is minimal. Simply purchase QR Stickers, download the free mobile app, and start attaching the stickers to items for scanning into your inventory. As you progress, enter details such as Location, Container, Item Type, and other relevant field information. For equipment with UPC or EAN codes, Scanlily accelerates the process by enabling you to scan the barcode to automatically populate descriptions, images, and other product details from a database of over 500 million products.
Tailor access rights as you add users
Adding users can be done simultaneously with inventorying. This step involves grouping users and assigning them appropriate permissions for item access and bookings. This approach ensures that users can only access equipment and functions pertinent to their roles, thus preserving the integrity and efficiency of the system. Scanlily makes this process intuitive by granting access rights based on item category. Unlike other systems that necessitate continuous permission assignment for each new item, Scanlily’s method lets new items within a category automatically inherit the pre-set access permissions. Likewise, new users in a designated group will receive access rights corresponding to that group.
Set up the booking system and perform training
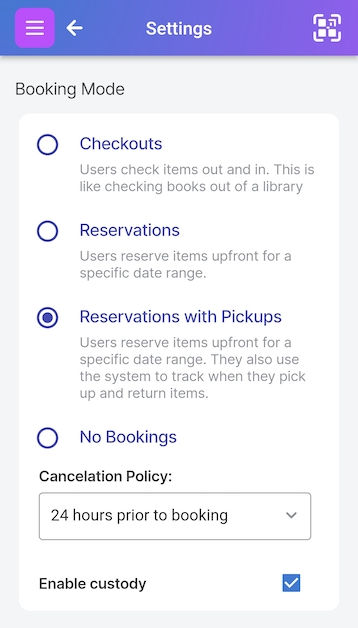
Most equipment management systems integrate various booking modes into a single user interface, which might necessitate additional training for your users. Plan to dedicate adequate time for this training. Scanlily simplifies this aspect by enabling you to select the most suitable mode for your business needs, reducing the need for user training.

Implement asset flags
An enterprise asset management system, such as Scanlily, allows setting flags to indicate item status (for example “Broken” and “Needs Maintenance ''). Select what flag values you’d like to display and set any alerts - for example, get alerted when an item is flagged as broken.
Develop an inventory of spare parts
Maintain a stock of essential spare parts to quickly address repairs and reduce downtime. In Scanlily, you can use the Quantity + / - feature to adjust stock levels. Additionally, Scanlily’s Quantity Alert feature can notify you when stock levels drop below specified thresholds.
Implement theft and loss prevention techniques
Encourage the return of lost items by adding “Scan if Found” QR stickers to items. Scanlily’s access control features further secure your equipment by restricting access to authorized personnel, providing an extra safeguard against unauthorized bookings, particularly for high-value items.
3. Ongoing Equipment Management System Usage, Maintenance and Training
As we delve into ongoing management, maintenance, and training, the focus is on leveraging the capabilities of your equipment management system to its fullest. Regular interaction with the system, particularly the dashboard, is a simple yet effective practice. The following are proactive steps for maintaining your equipment inventory. A proficient system like Scanlily also enables a more reactive approach by sending alerts for maintenance needs or overdue returns, reducing the need for constant vigilance.
Check the Dashboard daily
Enterprise asset management systems feature user-friendly dashboards with key indicators for daily checks. These assist in assessing the general status of your equipment and deciding on necessary actions. With Scanlily, for example, use the map feature to locate your items easily.
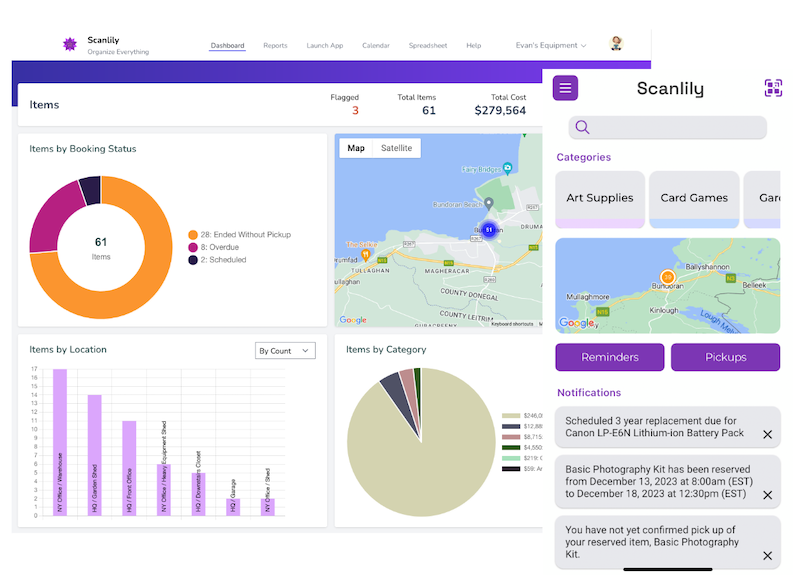
Capture costs and maintenance reports related to items
Track not only the original costs of your equipment but also simplify the collection of ongoing cost and maintenance records using your management system. Scanlily streamlines this process with its Attachments feature. Simply take a photo of the original item receipt or maintenance/repair receipts and attach them to the item's record. This method ensures easy access to receipts for returns. Furthermore, all other maintenance documents are accessible and timestamped for future reference
Leverage the reporting and online Spreadsheet for inventory management
An enterprise asset management system like Scanlily and its peers have robust and flexible reporting features. Leveraging them on an ongoing basis for a variety of purposes is a key to success in equipment management. Furthermore Scanlily’s online spreadsheet feature adds the efficiency of combined reporting and change capability. This dual functionality streamlines the process of keeping your inventory data accurate and up-to-date.

Conduct regular maintenance and inspections
Ensure all equipment undergoes routine maintenance and inspections to prevent breakdowns and extend its useful life [‘]. You can designate custom fields for the item types being maintained to indicate maintenance status. Alternatively, and perhaps more efficiently, you can take a photo of and print an inspection report or attach a PDF to the item using Scanlily’s Attachment feature.
Provide ongoing training for equipment use
Offer training to staff on the correct use and safety procedures of equipment. In Scanlily, because the QR stickers are also URLs, they can be affixed to equipment and users can scan them to obtain training materials and videos using a mobile device even without the use of an app.
Maintain ongoing loss prevention strategies
Implement a protocol where personnel scan items each time they are moved to a new location, enabling tracking them on a map. This aids in monitoring the whereabouts of assets. Additionally, enforcing a booking agreement and signature page through Scanlily can foster a sense of responsibility in borrowers, encouraging better care of the items.

4. Performance Review and Continuous Improvement
In this phase, the goal is to convert the data collected from your equipment management system into actionable insights for your organization.
Manage equipment costs effectively
Use asset management reports to monitor and control the expenses related to equipment purchase, maintenance, and operation. Use the system to reference not only the original equipment cost but the maintenance costs as well. With advancements in AI, expect more automation in this reporting, enhancing efficiency. Regularly analyzing these reports can pinpoint potential areas for cost reduction, revealing spending patterns and aiding in informed resource allocation.
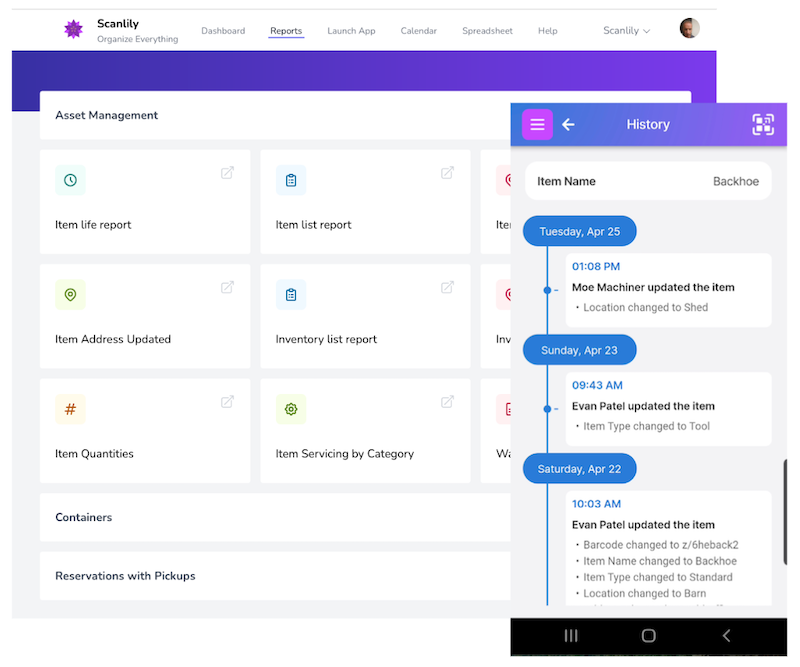
Prioritize equipment upgrades based on usage data
Prioritizing equipment upgrades based on usage data is a data-driven approach to maintaining an efficient inventory. By evaluating equipment performance data, you can identify which items are most frequently used, which are nearing the end of their useful life, and which might require upgrades or replacements. This approach ensures that investment in new equipment is made strategically, focusing on areas that will bring the most value to your operations. Scanlily's detailed usage reports can be instrumental in this process, providing the necessary data to make well-informed decisions.
Use the item History
Take advantage of Scanlily's History log feature to inform and learn from usage patterns and locations. This feature allows you to track where an item has been and when it has been updated. This historical data can help predict future equipment needs and identify potential issues before they become major problems.
Perform regular audits
Regularly evaluate your equipment management practices to uncover areas for enhancement. Periodic audits are key to maintaining an effective and efficient management system, ensuring that all processes are optimized and aligned with organizational goals.
Encourage a collaborative environment for feedback
Create a culture where feedback from various team members is used to refine equipment management strategies. Add fields to selected item types for this purpose. Employ Scanlily's user access control features to facilitate collaborative equipment management and feedback gathering in a manner that doesn’t compromise data.
5. Conclusion - Best Practices in Equipment Management
This guide has covered key steps: from initial planning to ongoing management, maintenance, and strategic improvement, highlighting the usefulness of a structured, technology-driven approach.
Nowadays, whether or not your job title is 'Equipment Manager', you have the opportunity to elevate your equipment management capabilities significantly. By adopting these strategies, your approach to equipment management can bolster your organizational objectives. With Scanlily, you gain access to a user-friendly and cost-effective tool that supports every phase of this process, simplifying and enhancing equipment management tasks.
Comments